انواع خدمات فنی و مهندسی شامل:
جوشکاری ، بریزینگ ، ماشین کاری دقیق ، تولید قطعات خاص ، مهندسی معکوس ، طراحی ، نقشه کشی ، اتوماسیون ، طراحی مدار ، طراحی هیدرولیکی و مکانیزه کردن در شرکت سامان صنعت انجام می پذیرد.
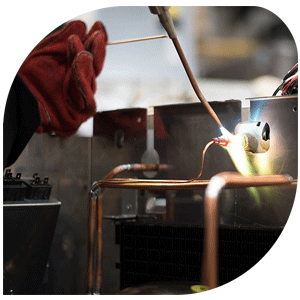
جوشکاری بریزینگ به فرایندی اطلاق میگردد که طی آن قطعات استیل به وسیله فیلر میلهای از جنس برنز و یا برنج به یکدیگر متصل میگردند وسایل و تجهیزات مورد نیاز برای این فرایند همانند بریز کاری معمولی میباشد با این تفاوت که در جوش بریز به دمای بیشتی نیاز میباشد که معمولاً توسط سوختن گاز استیلن تأمین میگردد. نام جوشکاری از این لحاظ بر روی این فرایند نهاده شده که طی آن حرکت مویینگی اتفاق نمی افتد.
اطلاعات بیشتر
از مزایای جوشکاری بریزینگ نسبت به جوشکاری ذوبی معمولی میتوان به موارد ذیل اشاره نمود
جوشکاری برزینگ امکان اتصال فلزات غیر همسان را میدهد و همچنین به پیشگرم بالا نیازی نداشته و تغییر شکل ناشی از دمای بالا در آن صورت نمیپذیرد.
انواع جوشکاری لیزری
۱ـ جوشکاری هدایتی
۲ـ جوشکاری نفوذی یا سوراخ کلیدی
تفاوت اساسی در این دو حالت آن است که در حالت اوّل سطح ناحیه جوش شکسته نمیشود و در حالت جوشکاری نفوذی سطح ناحیه جوش باز میشود تا باریکه لیزر به درون ناحیه مذاب نفوذ کند.
حالت جوشکاری هدایتی نگرانی کمتری بخاطر عدم نفوذ لیزر به درون ماده ایجاد میکند در نتیجه جوشکاری هدایتی کمتر مستعد جذب گاز در هنگام جوشکاری است. در جوشکاری نفوذی بسته شدن غیرپیوسته سوراخ کلید منجر به تشکیل تخلخل در جوش میشود. حالتهای هدایتی و نفوذی در جوشکاری نقطهای به یکدیگر تبدیل میشوند که این به شدّت قله توان لیزر و عرض پالس بستگی دارد.
سوراخ کلید توسط لیزر معمولاً برای فولاد در چگالی توان تقریبی اتفاق میافتد. در چنین حالتی جوش کم عمق و پهن است. امّا در چگالی توانهای جوشهایی عمیق و نازک که زمان برهم کنش کمتری نیاز دارد بدست میآید که این اجازه جوشکاری با سرعت بیشتر را میدهد. از آنجا که جوشکاری لیزر یک روش با چگالی انرژی بالا است نیازبه هدایت گرما برای ایجاد نفوذ عمیق ندارد و این برخلاف روشهای معمول و مرسوم جوشکاری قوس و گاز است که از طریق هدایت گرما به نفوذ دست مییابند.
در حالت جوشکاری هدایتی مدارهای همدما بصورت یکسان و با فاصله یکسان از منبع قرار دارند. عرض جوش در این حالت معمولاً بزرگتر از عمق و انرژی ورودی بیشتر از مقدار لازم برای نفوذ است. در حالت سوراخ کلید یا نفوذی منبع حرارت لیزر از سطح به داخل ضخامت ماده منتقل میشود و جوش عمیق و نازک بوجود میآید. همچنین در این حالت مقدار گرمای ورودی به حداقل میرسد.
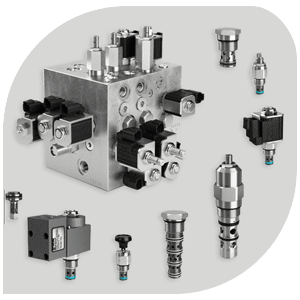
ضرورت تولید قطعات خاص و با کیفیت برای تولید شیرهای هیدرولیک ما را بر آن داشت که خط ماشینکاری خود را ارتقا داده زمینه تولید انواع قطعات پیچیده و خاص را در نظر بگیریم. با استفاده از تکنولوژی روز دنیا و بهره گیری از متخصصین مجرب توانسته ایم علاوه بر تامین نیاز شرکت ، سفارشات را نیز پاسخگو باشیم.
اطلاعات بیشتر
يكي از حلقه هاي گمشده صنعت كشور بخش طراحي و دانش فني قطعات يا ماشين آلات در دست ساخت ميباشد. در مهندسي معكوس كه بطور فزاينده در کشورهای در حال توسعه مورد استفاده قرار ميگيرد و در كشور ما نيز مرسوم است، متاسفانه انجام عمليات طراحي و محاسبات مهندسي و تهيه دانش فني قطعات ناديده انگاشته ميشود، كه خود يكي از دلايل اصلي عدم كيفيت قطعات و حتي در بعضي مواقع باعث غير اقتصادي بودن قطعه توليد شده ميگردد. زيرا اغلب در مهندسي معكوس، قطعه يا مجموعه قطعات يك ماشين در دست بوده و سازنده بدون توجه به عملكرد قطعات و وظايف آنها با يك مرحله اندازه گيري و انتخاب يك متريال مشابه به قطعه اصلي شروع به ساخت آنها مي نمايد. بسيار اتفاق افتاده قطعه يك ماشين ساخت يك كشور اروپايي كه به دلايلي فرسوده شده مورد ساخت مجدد به روش ماشينكاري قرار ميگيرد و نمونه آن بوسيله تراشكار ساخته مي شود، اما قطعه كپي شده داراي طول عمر و توان عملكرد قطعه اصلي نمي باشد. تمامي اين مشكلات به علت عدم انجام محاسبات مهندسي صحيح و نداشتن دانش فني قطعه مي باشد.
ما در شرکت سامان صنعت پویا تمامي روشهاي مهندسي در بخش طراحي ، تحليل ، و شبيه سازي هاي مهندسي را بطور كاملاٌ حرفه اي و موثر به منظور ساخت قطعات مورد سفارش بكار مي گيریم و حتي در بعضي مواقع كه مشتري نيازي به دانش فني قطعه ندارد و هدف او دستيابي به يك قطعه با استحكام و با كيفيت است. ما وظيفه خود ميدانيم كه قبل از ساخت ابتدا تا حد لازم عمليات طراحي و محاسبات تنشي وارد بر قطعه را انجام داده و پس از دستيابي به يكسري داده هاي محاسبات مهندسي ، روش ساخت قطعه را باز نويسي نموده و سپس اقدام به ساخت قطعه نماييم، طوري كه به قطعه كاملاٌ مطلوب دست يابیم.
مجموعه فعاليتهاي ساخت شامل طيف گسترده اي از عمليات مختلف ماشين كاري ميباشد. در اختيار داشتن انواع ماشين ابزار هاي سي ان سي (CNC) و ماشين ابزار هاي معمولي(Manual) در رنج هاي مختلف و تجهيزات ديگر مانند دستگاه هاي برش ليزر و جوش و همچنين دارا بودن دستگاه CMM اين امكان را به ما ميدهد كه توانايي ساخت هر نوع قطعه از ساده تا بسيار پيچيده با دقت بالا را داشته باشيم. لذا از توليد تكي قطعات گرفته تا انبوه قطعات بصورت سري به آساني براي ما امكان پذير است.
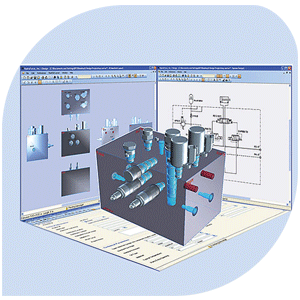
مهندسی معکوس یکی از روشهایی است که شرکتها با به کارگیری آن، فرایند تکوین محصول خود را سرعت می بخشند. این روش در کشورهای درحال توسعه چون ایران که ازنظر دانش طراحی محصول و فناوری تولید عقب تر از کشورهای پیشرفته هستند، پاسخی به افزایش توان طراحی و تسریع فرایند تکوین است.
اطلاعات بیشتر
مهندسی معکوس برای بازیابی و تشخیص اجزای متشکله یک محصول بویژه در صورت عدم دسترسی به طراحی اولیه کاربرد داشته و برای نگهداری، گسترش و توسعه امکانات موجود و مهندسی مجدد (RE-ENGINEERING) مورداستفاده قرار می گیرد.
این روش ، روش پذیرفته ای برای کشورهای درحال توسعه به شمار می رود. در این فرایند ابتدا میزان کمبود اطلاعات فنی برای پشتیبانی از تولید یک محصول معین می شود. سپس با انجام یک کار تیمی منسجم، متشکل از متخصصان و محققان رشته های مختلف علوم پایه به همراه مدیریت و سازماندهی مناسب تشکیلات تحقیقاتی و توسعه ای (R&D) سعی می شود مدارک و نقشه های خاص طراحی محصول به دست آید. با درنظر گرفتن مشخصات، هدف و شرایط طراحی محصول، استانداردهای ملی و رایج و همچنین پوشش دادن نقاط مجهول و ناشناخته سعی می شود مراحل نمونه سازی و نیمه صنعتی و در صورت لزوم ساخت و تولید محصول، انجام گردد.
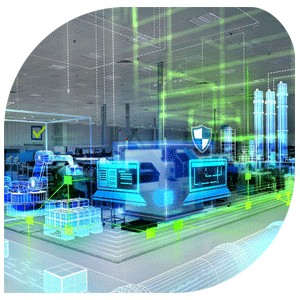
اتوماسيون صنعتي به بهره گيري از رايانه ها بجاي متصديان انساني براي كنترل دستگاه ها و فرايندهاي صنعتي گفته ميشود. اتوماسيون يك گام فراتر از مكانيزه كردن است . مكانيزه كردن به معني فراهم كردن متصديان انساني با ابزار و دستگاه هايي است كه ايشان را براي انجام بهتر كارشان ياري ميرساند. نمايانترين و شناخته شده ترين بخش اتوماسيون صنعتي ربات هاي صنعتي هستند.
اطلاعات بیشتر
امروزه كاربرد اتوماسيون صنعتي و ابزار دقيق در صنايع و پروسه هاي مختلف صنعتي به وفور به چشم مي خورد . كنترل پروسه و سيستمهاي اندازه گيري پيچيده اي كه در صنايعي همچون نفت ، گاز ، پتروشيمي ، صنايع شيميايي ، صنايع غذايي ، صنايع خودرو سازي و غيره بكار مي آيد نيازمند ابزارالات بسيار دقيق و حساس مي باشند . پيشرفتهاي تكنيكي اخير در كنترل فرايند و اندازه گيري پارامترهاي مختلف صنعتي از قبيل فشار ، دما ، جريان و غيره باعث افزايش كيفيت محصولات و كاهش هزينه هاي توليد گرديده است.
در حال حاضرارتقاء سطح كيفي محصولات توليدي در صنايع مختلف و در كنار آن افزايش كمي توليد ، هدف اصلي هر واحد صنعتي مي باشد و مديران صنايع نيز به اين مهم واقف بوده و تمام سعي خود را در جهت نيل به اين هدف متمركز نموده اند . لازمه افزايش كيفيت و كميت يك محصول ، استفاده از ماشين آلات پيشرفته و اتوماتيك مي باشد . ماشين آلاتي كه بيشتر مراحل كاري آنها به طور خودكار صورت گرفته و اتكاي آن به عوامل انساني كمتر باشد . چنين ماشين آلاتي جهت كاركرد صحيح خود نياز به يك بخش فرمان خودكار دارند كه معمولا از يك سيستم كنترل قابل برنامه ريزي (به عنوان مثال PLC يامدار منطقي قابل برنامه ريزي) در اين بخش استفاده ميگردد . بخش كنترل قابل برنامه ريزي مطابق با الگوريتم كاري ماشين ، برنامه ريزي شده و ميتواند متناسب با شرايط لحظه اي به عملگر هاي دستگاه فرمان داده و در نهايت ماشين را كنترل كند .
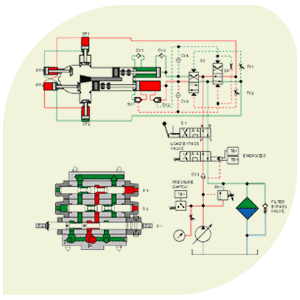
یک مدار ساده هیدرولیک ؛ شامل یک عملگر ( جک – سیلندر ) ؛ شیر فرمان و یک پاور پک ساده که شامل : پمپ ؛ الکترو موتور ؛ فشار شکن و … است را در نظر می گیریم .
اطلاعات بیشتر
طراحی مدار های هیدرولیک
مدار ساده هیدرولیک ؛ شامل یک عملگر ( جک – سیلندر ) ؛ شیر فرمان و یک پاور پک ساده که شامل : پمپ ؛ الکترو موتور ؛ فشار شکن و … است را در نظر می گیریم .
جهت طراحی این مدار مراحل ذیل را طی می نماییم
۱- ابتدا باید نیروی مورد نیاز را که قرار است توسط جک تولید شود ؛ برآورد و یا محاسبه نماییم (با توجه به کاربرد جک )
۲-انتخاب فشار کاری سیستم هیدرولیک ؛ با توجه به جدول فشارهای استاندارد در مدارات هیدرولیک و نیز فشار پمپهای هیدرولیک موجود در بازار و نهایتا قیمت تمام شده قطعات ؛ فشار کاری انتخاب می گردد .
انتخاب فشار که منجر به انتخاب پمپ ؛ الکترو موتور و شیرها و… می گردد باید به گونه ای انجام شود که نهایتا سیستم ضمن انجام کاری که به عهده آن است ؛ ارزان و اقتصادی نیز باشد .
کلا توصیه می شود تا حد امکان فشار زیر ۲۰۰ bar انتخاب شود . اگر چه سیستمهای هیدرولیک تا فشار ۷۰۰ bar و حتی بیشتر وجود دارد اما عملا هزینه های قطعات ؛ از فشار ۲۰۰ به بالا به صورت تصاعدی بالا می رود و فقط وقتی مجبور هستید ؛ از فشارهای بالاتر استفاده کنید .
-۳ با مشخص شدن نیرو و فشار کاری سیستم می توان قطر سیلندر ( جک ) را محاسبه نمود قطر محاسبه شده را باید به اعداد قطر لوله های بدون درز و سنگ خورده که در بازار موجود می باشد و مخصوص ساخت جک است ؛ رند نمود .
هنوز طراحی سیلندر تمام نشده است و محاسبه قطر rod باید بر مبنای نیروی سیلندر که توسط rod اعمال می شود انجام گیرد . محاسبه قطر rod باید به گونه ای باشد که از کمانش rod در زمان اعمال حد اکثر نیرو جلوگیری کند
.
۴- انتخاب و محاسبه پمپ : سه نوع پمپ در طراحی مدارات هیدرولیک صنعتی استفاده می شود الف ) پمپهای پیستونی : عموما برای فشارهای با استفاده می شود و لذا گران می باشند . ب) پمپهای دندهای ج) پمپهای پره ای .
این دو نوع اخیر برای فشارهای کم و متوسط استفاده می شوند و در دبی های مختلف و تنوع زیاد با قیمتهای مناسب در بازار موجود می باشد .
جهت انتخاب پمپ باید علاوه بر فشار مورد نیاز دبی را نیز برآورد کرد . دبی سیستم به عملگر مدار ( اینجا جک هیدرولیک ) بستگی دارد . برای محاسبه روغن مصرفی جک : حجم قسمت جلو و عقب جک را محاسبه می کنیم حال مجموع این دو عدد را در تعداد عملکرد جک در هر دقیقه ضرب می کنیم ( این تعداد با توجه به کاربرد جک مشخص می شود . ) حاصل لیتر بر دقیقه و یا دبی پمپ است . حال فقط کافی است با معلوم بودن فشار و دبی ؛ مناسبترین پمپ از سه نوع فوق الذکر را انتخاب کرد توجه به این نکته ضروری است که معمولا در بازه های وسیعی مشخصات انواع پمپ با هم همپوشانی دارند و نهایتا این قیمت است که پس از مشخصات فنی منجر به انتخاب پمپ می شود .
باید توجه داشت که محاسبه دبی از اهمیت زیادی برخوردار است زیرا اگر دبی کم برآورد شود ؛ مدار سرعت لازم را نخواهد داشت و اگر دبی بیش از اندازه مصرف باشد ؛ باعث گرم شدن روغن می شود که مشکلات زیادی را به وجود می آورد .
۵- محاسبه الکترو موتور : با توجه به مشخصات بدست آمده جهت پمپ یعنی دبی و فشار ؛ توان پمپ قابل محاسبه می باشد . توان الکترو موتور از نظر تئوریک با توان پمپ برابر است ؛ اما در عمل اندکی بیشتر ( ۱۰% تا ۲۰% ) در نظر گرفته می شود .
۶- محاسبه سایز لوله و شیلنگها ( قطر داخلی) : عموما دیده می شود که به این بخش توجه کمتری صورت می گیرد ؛ در حالی که از اهمیت زیادی برخوردار است .
اگر قطر لوله کمتر از مقدار مورد لزوم باشد ؛ لوله مانند یک گلویی عمل کرده و فشار بالا می برد دبی و در نتیجه سرعت سیستم کاهش می یابد ؛ فشار اضافی به پمپ و الکترو موتور وارد می شود که استهلاک را افزایش می دهد و مصرف انرژی نیز افزایش می یابد .
در کتب و مراجع هیدرولیک ؛ توصیه های سرعت روغن جهت خطوط مختلف انتقال روغن مانند خط فشار ؛ خط برگشت و خط تخلیه ؛(با توجه به فشار کاری سیستم) ارائه شده است .
با استفاده از این توصیه های سرعت و نیز معلوم بودن دبی ؛ با محاسباتی ساده قطر داخلی لوله (یا شیلنگ) محاسبه می گردد .
لوله های هیدرولیک بدون درز موجود در بازار دارای قطر استاندارد می باشند که باید قطر محاسبه شده خود را با اندازه سایز این لوله ها هماهنگ نماییم ؛ توصیه میشود اگر اندازه محاسبه بین دو عدد سایز لوله بدست آمد ؛ لوله با سایز بزرگتر انتخاب گردد .
۷- اندازه پاور پک : حجم روغن پاور پک ۲ تا ۳ برابر دبی پمپ بر حسب Lit / Min در نظر گرفته می شود و حجم کل پاور پک ۱٫۱۵ تا ۱٫۳ برابر حجم روغن در نظر گرفته می شود .
۸- شیر های راه دهنده و کنترل فشار و کنترل دب : این شیرها با توجه به فشار کاری سیستم ؛ و دبی عبوری از آن انتحاب می گردند . در مارکها ی بسیار گوناگون و از کشورهای مختلف در بازار عرضه می شوند ؛ و قیمتهای آنها نیز بسیار متنوع می باشد ؛ که با توجه به بوجه پروژ مارک قطعات انتخاب و خریداری می گردد .
نکته دیگری که در انتخاب شیر ها مهم می باشد : نحوه نصب شیر می باشد که قبل از خرید باید مشخص گردد که نحوه نصب آن : بلوکی ؛ بین راهی ؛ کارتریجی و … می باشد و نیز کنترل شیر برق یا دستی یا پنوماتیک یا … است
با توجه به مجموع این محاسبات ؛ مشخصات قطعات معلوم گردیده و می توان خرید و پس بستن مدار را انجام داد .
مطالب گفته شده اگر چه مربوط به یک مدار ساده هیدرولیک می باشد ؛ لیکن مفاهیم آن جامعیت داشته و اصول کلی آن حتی در مدارات پیچیده نیز صدق میکند .
شرکت سامان صنعت پویا به واسطه نزدیک به دو دهه فعالیت در زمینه هیدرولیک و داشتن متخصصین مجرب قادر است سیستم و مدارهای هیدرولیکی مورد نیاز شما را به راحتی طراحی و اجرا نماید. مشاورین ما همواره آماده پاسخگویی به سولات فنی شما می باشند ، برای اطلاعات بیشتر با متخصصین ما در تماس باشید.